Posts
Showing posts from 2017

Posted by
Elmer Nahum
Miter Clamp Assisted Marking of Pin Board
- Get link
- X
- Other Apps

Posted by
Elmer Nahum
Portable Miter Box and Tenon Cutter
- Get link
- X
- Other Apps

Posted by
Elmer Nahum
Easy Add-On Tail Vise for the Tiny Shop
- Get link
- X
- Other Apps
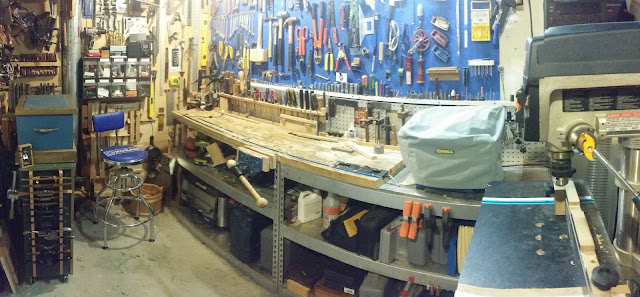
Posted by
Elmer Nahum
Enjoying Woodworking in a Tiny Workshop
- Get link
- X
- Other Apps